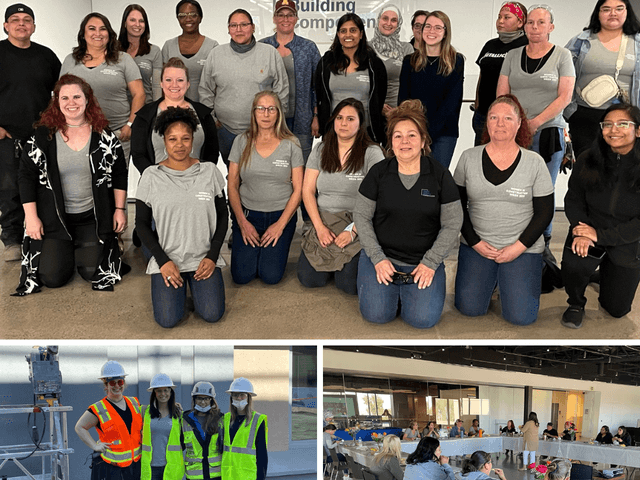
Celebrating Women in Construction Week 2022 – (read more)
Digital Building Components is proud to celebrate Women in Construction Week from March 6-12!
At Digital Building Components, we roll our studs in-house. But how does this benefit your next project?
Our processes revolve around transforming virtual models into precise-to-spec building components. Because the planning phase is crucial, Digital Building Components works with our clients to develop the best course of action. Before manufacturing begins, our design team identifies the prefabrication path using DfMA (Design for Manufacture and Assembly) methodology. Project customization options are readily available for each component made at our facility.
Once designs are finalized, the schematics are sent directly to our plant floor’s roll former – where each project begins. This automated design-to-manufacturing process maximizes efficiency by reducing time and eliminating potential communication errors. Digital Building Components uses unique patented software to fabricate each design, ensuring a perfectly rolled stud and other components for each project.
Each stud is ‘made-to-order,’ precisely measured, and cut. This significantly reduces material and labor costs on and off the job site. After each stud is formed, our employees perform a visual inspection and guide it onto the next phase for panel production. We regularly perform quality assurance measurements on all our equipment to meet production standards and expectations.
Lean manufacturing concepts are integrated into each step of our design, fabrication, and installation processes. Detailed data and information from each phase, including stud rolling, is collected and used to continuously improve project processes and overall execution.
Take on a unique build approach with prefabrication that changes the way you build. If you’re a contractor or developer and want to learn more about how prefabrication methods can benefit your next build, please visit our Contact Page and message us!
Keep Reading
Digital Building Components is proud to celebrate Women in Construction Week from March 6-12!
Digital Building Components creates digitally prefabricated structures that streamline construction processes and minimize timelines. But how exactly do we achieve reliable, rapid delivery and installation?
The Digital Building Components app streamlines the communication process while enabling earlier and more detailed installation sequencing.