The Proof is in the Numbers: 1,000 Days of Zero Safety Incidences
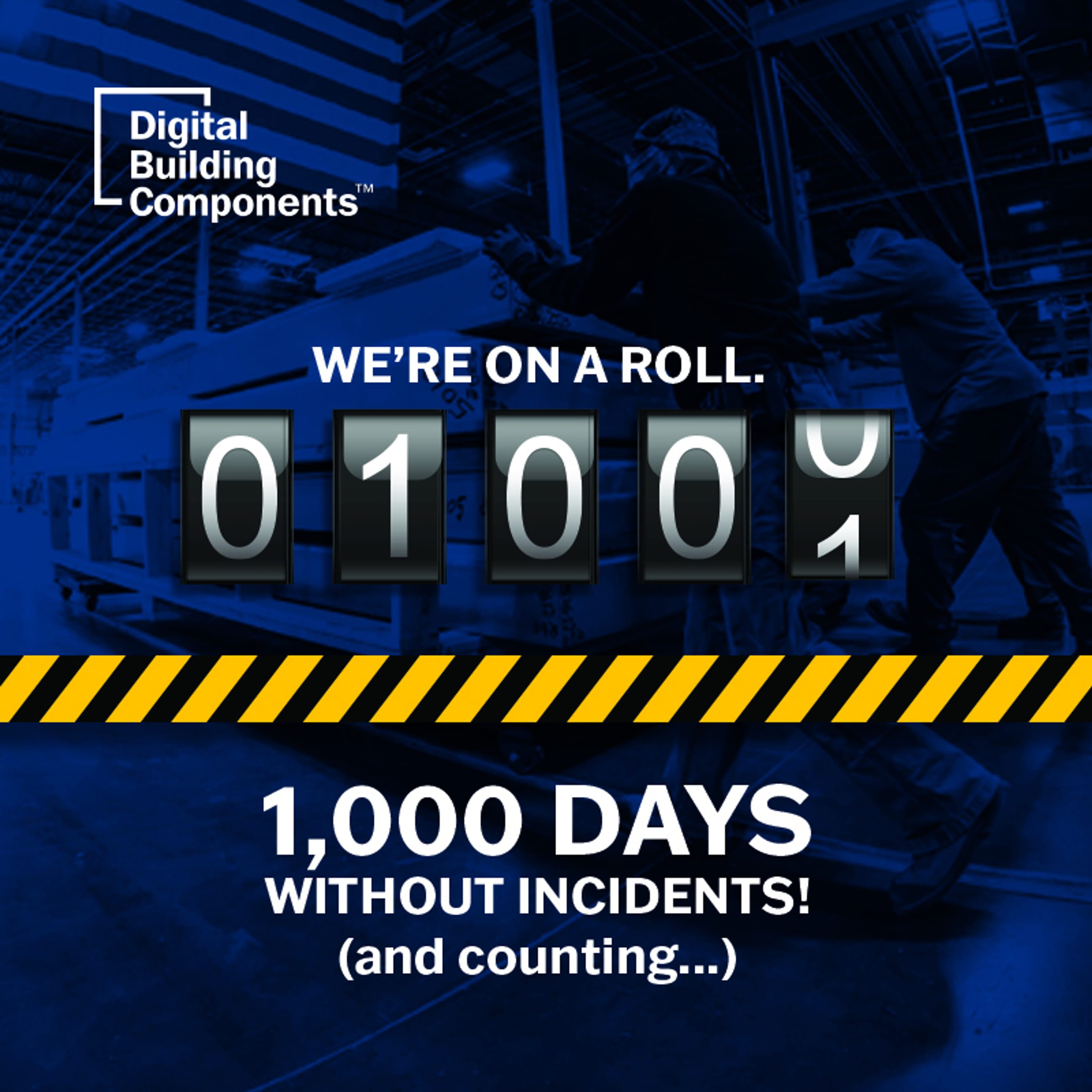
Some of the most alarming statics in the construction industry center around safety incidences. According to the Occupational Safety and Health Administration (OSHA), approximately 20% of worker fatalities took place in the field of construction, “accounting for one in five worker deaths for the year.” Further underscoring jobsite risk, the accident rate is on average 71 percent higher than in other industries, resulting in workers’ compensation claims that hover around an estimated $2.5 billion.
Understanding the substantial risk to employee health and wellbeing, Digital Building Components has geared its operations and day-to-day protocols around safety from day one. Freed from the limitations of traditional construction methods, we’ve been able to tailor our digitally native prefab methods to eliminate unforeseen variables like inclement weather and overhead hazards while still producing technically challenging and customized wall systems.
The results are paying off. As a company, we’ve gone 1,000 days with zero safety incidences. That’s more than 30 months or two and half years of our team going to work and returning home safely.
How will we continue prioritizing safety?
- Leverage advancements in technology – by integrating the latest technology into our operations, we minimize the risk of human error and injury-inducing miscommunications. In fact, our computer-controlled systems and patented software programs are designed to identify and autocorrect mistakes that may otherwise endanger the safety of trade workers.
- Alleviate injuries through automation – precarious tasks such as cutting, measuring and welding are all done through the power of automation. These automated systems can also analyze a project, from its size and spacing to bracing mechanism, ensuring equipment at every stage can support the panel to minimize operation accidents.
- Create predictable outcomes – all digitally native work is done upfront and easily integrated into Revit models to create predictable outcomes, from prefabrication and shipping all the way to installation. There are no surprises in the field, and our integrated software programs and apps even make it possible to track the entire construction progress.
- Maintain a well-lit and employee-centered factory environment – not only do all operations take place at ground-level, but our open factory environment also allows safety measures to be easily monitored and implemented. With clear pathways, ergonomic stations and a well-lit, controlled interior, we also ease congestion and the safety incidents that often accompany traditional construction methods.
If you’re interested in joining our team or learning more about how we can partner with you to increase the safety of your next project, contact us!