How a Prefab Approach Can Solve Common Jobsite Constraints
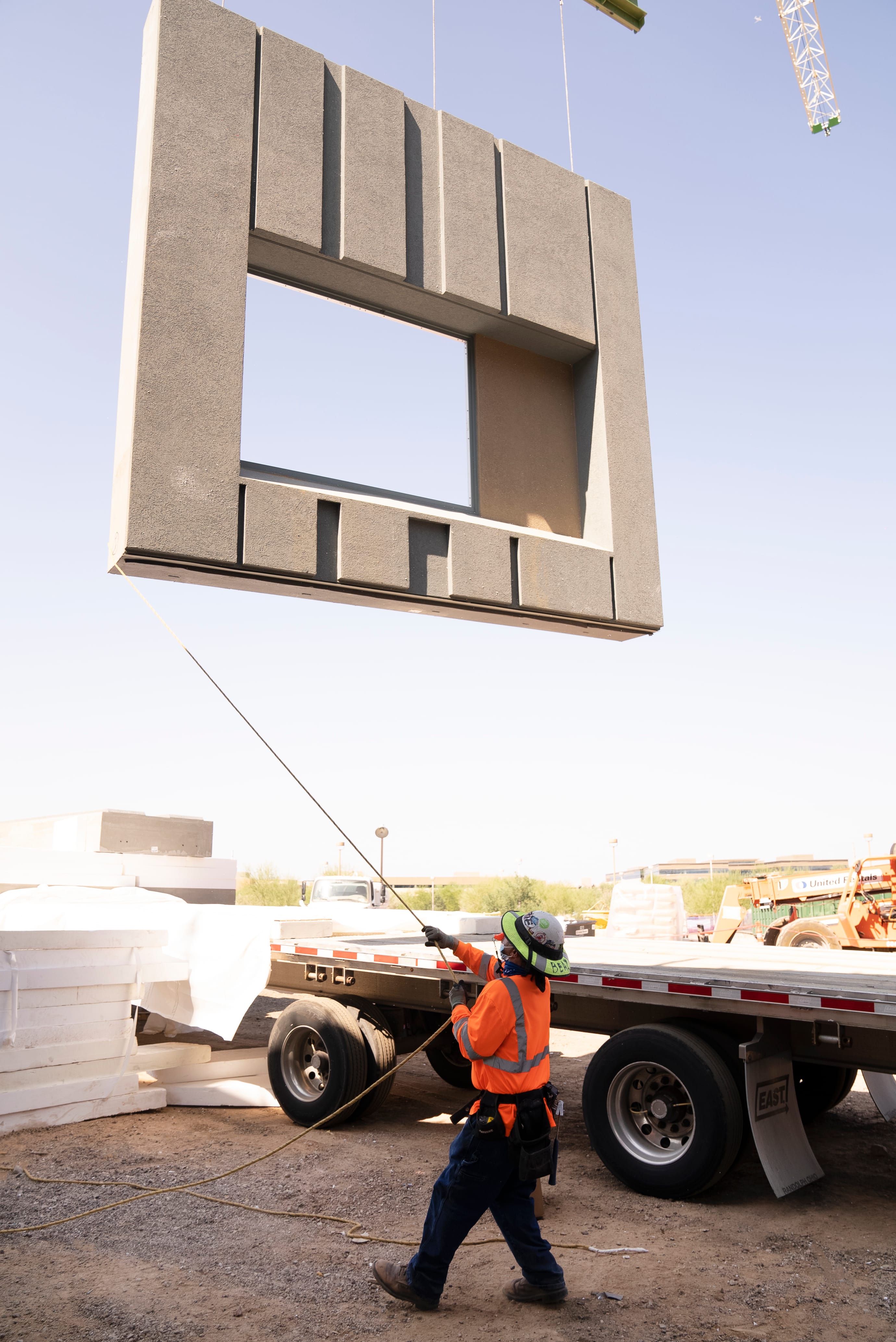
From site-specific restrictions like noise ordinances to general issues like labor and material shortages, there are several impediments that can slow a construction project. In fact, the McKinsey Global Institute’s report indicates the construction industry lags behind other industries in terms of productivity. Much of this can be attributed to traditional jobsite operations. Four common construction constraints include:
- Skilled labor shortages
- Safety concerns
- Environmental constraints
- Material shortages and handling
A prefabricated construction approach can help mitigate these issues for more efficient builds.
- A shortage of skilled laborers has been one of the most cited problems in construction. As more senior laborers retire and fewer people enter the field, the pool of skilled laborers is steadily shrinking. Now, almost all contractors report difficulty finding skilled workers. Prefabrication reduces the need for on-site skilled laborers as patented software, automatic equipment and trained trades work together to accomplish more with less in a controlled manufacturing setting. Also, many prefabricated companies provide skills training for those new to the industry, including those traditionally excluded from construction.
- Safety is without question a big concern in construction. According to the Occupational Safety and Health Administration, the construction industry’s accident rate is 71% higher than other industries. While this affects workers and their families substantially, it also slows productivity on the jobsite since workers need on average 13 days away from work to recuperate. Prefabrication minimizes these issues with day-to-day protocols that promote worker safety. Controlled working environments also eliminate unforeseen variables (like inclement weather), making working conditions safer overall. As proof, Digital Building Components recently hit 1000 days without a safety incident.
- Environmental constraints like inclement weather, noise ordinances and congested work areas can slow construction to a crawl. These impediments are often unforeseen, which can easily spiral into downtime, supply chain issues and other delays. Because prefabrication sidelines most site-specific issues, it can alleviate these delays and other related ones as well. For instance, inclement weather could delay a framing crew, which would impact the timeline for electricians, glaziers, plumbers and more. Further setbacks as a result of this original delay could grow rather quickly. However, because prefab facilities can safely operate in any weather and at predictable times and speeds, they make the timeline to completion quicker and more reliable.
- Material shortages due to supply chain issues have plagued the construction industry the past couple of years, which has slowed construction, escalated material prices and limited what contractors can do. Beyond that, moving materials from one place to another on site to accommodate new shipments can further slow construction. A prefab approach allows manufacturers to build components in tandem to allow for just-in-time delivery. This makes it possible to lock in material pricing and helps mitigate material and installation delays. Also, because these products arrive on site ready for install, crews do not have to move materials to make room for multiple material shipments, which saves time over the entire project.
By helping contractors sidestep the above constraints, a prefab approach helps contractors do more with less. Navigating seen and unforeseen jobsite obstructions can mean the difference between done and delayed. If you’d like to learn more about how prefabrication can optimize your project, please visit our contact page for more information.