The Power of Quality Control on Prefab Outcomes An Interview with Digital Building’s Quality Control Manager
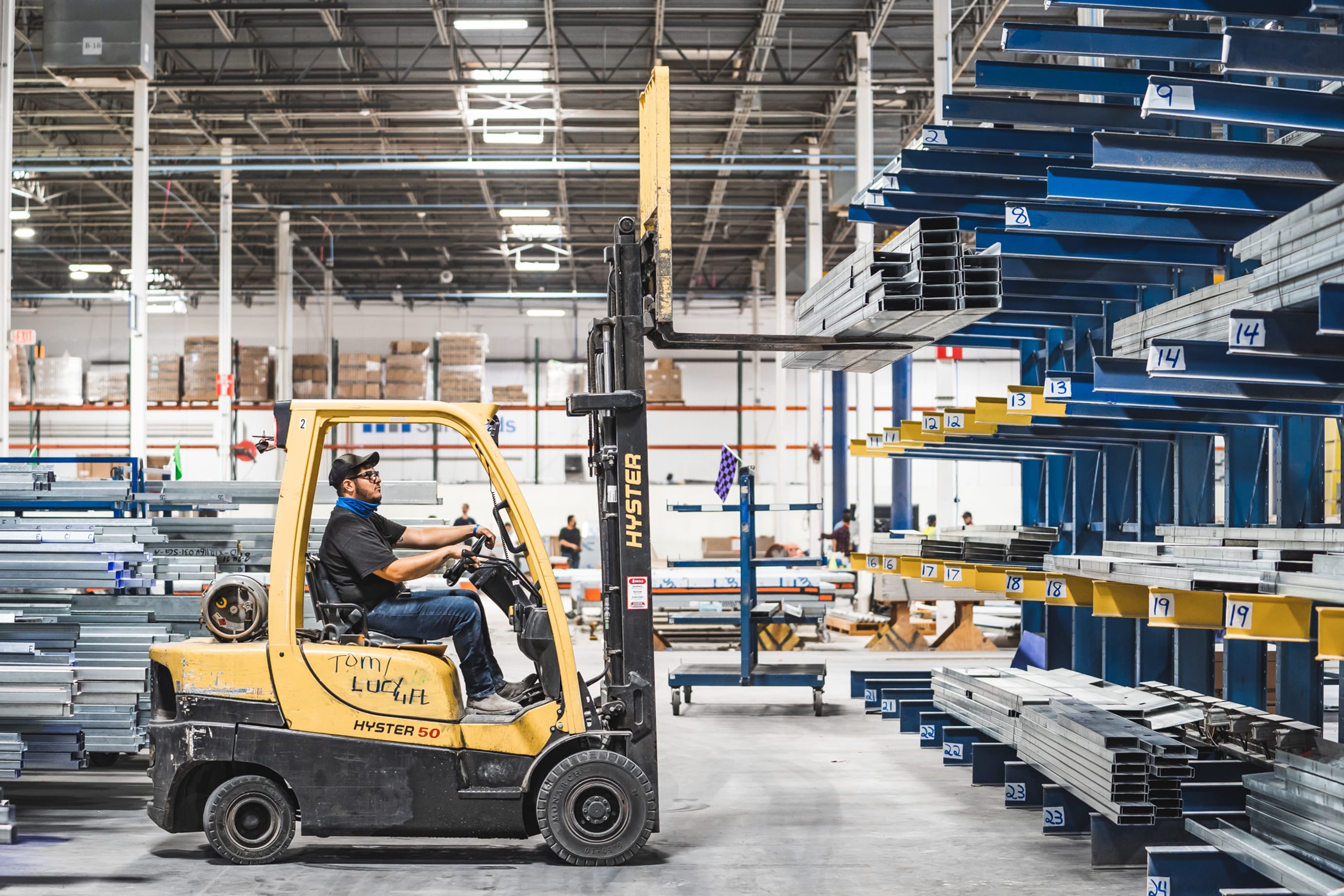
One of most desirable attributes of digital fabrication is that it ensures predictable outcomes. By transforming virtual models directly into precise-to-spec building components, materials are designed and fabricated to fit into the building architecture from a project’s onset. Exact components reduce the need for rework onsite. This, in turn, significantly improves product compatibility, install times and overall construction schedules.
While the digital fabrication process itself takes much of the credit for this time-saving predictability, one of the unsung heroes is quality control—a process we firmly believe in here at Digital Building Components. Throughout the day, the quality control team performs assurance measures and checks on materials with equipment to verify components are produced as expected. The intermediary between design and execution, they inspect and analyze each part and panel to ensure it meets code, will install as expected and perform as needed in the field. Given that 90 percent of Digital Building’s solutions are custom and designed to varying building requirements, this is no small task.
For a behind-the-scenes look at how the Digital Building team keeps quality control front and center as they assess project-specific solutions, we sat down with Jason Roland, QA/QC manager at Digital Building Components.
Q: Can you overview the quality control process at Digital Building?
A. “Digital Building’s proprietary software sends data from 3-D fabrication models directly to the roll forming equipment, which in turn handles all measuring, printing and cutting tasks. The components are then transformed into completed panels through a series of manual, automated and robotic processes, such as our robotic component welder. The quality control team works in tandem performing checks on these machines and materials, starting with roll-formed studs and tracks to sheathing and ending with exterior finishes. At each phase of prefabrication, we run through a series of quality checks, reviewing factors like overall length and width of the studs and track, waterproofing and exterior finishes and so on. After every phase of production there are a series of questions that must be completed, and images are taken in our easily accessible app on the quality team’s Ipads.
While automation is highly exact – for example, all of our studs and tracks are labeled with printed letter identifiers to show exact placement of materials before welding – we leave nothing to chance. Our goal is to ensure components are built correctly and with the quality needed for today’s high-performance buildings.”
Q. With tight construction timelines, how does Digital Building ensure speed is not compromised during quality control checks?
A. “Great question. The quality control team is working concurrently with the production team so as not to bog down the process. We let production drive the timing and then we come in alongside and do our quality control checks. We move through each phase of prefabrication together. Because of our streamlined process and digital tracking, our evaluations only take about 15 minutes or less depending on the complexity of the panel. We also do precheck work alongside production to keep things moving.”
Q. How does Digital Building implement quality control?
A. “We start with our team, making it a priority to ensure our quality control inspectors have the skillsets they need to succeed. That means continual training, in addition to having those with specialized skills focus is on areas within their wheelhouse. For example, inspectors with AWCI background will often work on waterproofing, base coat and mesh and different types of finishes, while those skilled in welding will typically visually inspect welds. Each inspector we hire is skilled and we leverage their knowledge to further what we can offer and inspect. We also work to ensure all of our quality control team members are cross trained over time to support efficiency. Each project is different, and we prioritize staying up on codes and standards to meet the industry’s demands.”
Q. Since each project varies, how do you work with building teams to meet their exact needs?
A. “Project inspections often vary by municipality, and some have adopted more stringent testing/requirements. Because of this, we work closely with the Inspector of Record (IOR) to accommodate the project’s exact needs. We can have an IOR come in and do an overview of the project with the quality control team at the onset of fabrication. Or we can work in tandem with the IOR or special inspector and meet with them at the factory multiple times a week, or as required.
The panels and project itself also dictate the level of engagement between the IOR and the Digital Building quality control team. Exterior finishes are often more involved, when you consider windows, metal panels, waterproofing and various other materials exposed to the elements. This is where having skilled and trained quality control inspectors comes into play.
To make it easier for all involved parties, Digital Building has also secured an IAPMO Certification, Smith-Emery Certifications, City of LA Certification and City of Phoenix Certification as an approved fabricator. This brings credibility to the entire Digital Building process and helps streamline efforts for IORs. Take IAPMO, its certification covers all our fabrication processes to ensure we not only follow industry standards but also building code requirements. Air + Water Barrier, welding, sheathing, studs and track gauges and sizes are all examples of things that are approved upfront. Because we are recognized as an approved fabricator, special inspections in the shop are not typically required.”
Q. What happens on the off chance the quality control team identifies an error?
A. “No company is 100 percent foolproof, and we take great care to identify any errors so that the final product goes out right. That’s the real value of quality control when we step in as a safeguard. We then go back, correct and rework the material or panel, as needed. We also take all findings and do a lessons learned review with our internal teams from the compiled data. We identify where the mistake came from and how it can be avoided in the future. This is key to advancing our process and products.”
Q. You’ve worked in the industry for 30 plus years. In your experience, what sets the Digital Building quality control process apart?
A. “There are a few things. First, we view quality control as a refined skillset. We aren’t just checking boxes; we have inspectors applying a great amount of expertise to advanced walls and panels. When you think about how building panels are used and what they may be exposed to or used for – from various weather conditions, which include earthquakes, wind loads and everything in between – we believe it’s essential to get them right.
We also rely on digital tracking. There’s no lost paperwork or bogged down communications. From the factory to the jobsite, we have digital access to the panel as it goes through the prefab process. We are also able to track via images and documenting should there be any issues. It’s a simple and effective way to communicate that we stand behind our work.”